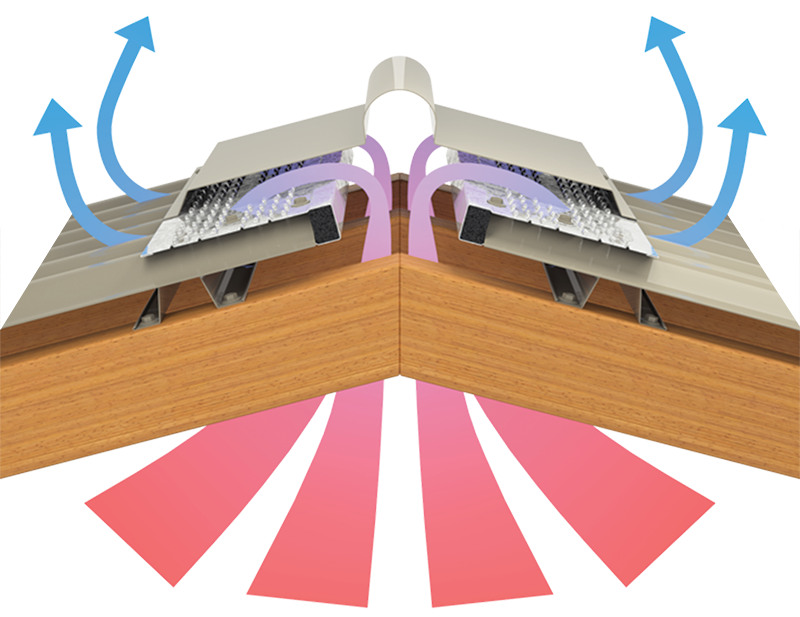
Introduction
VENT-A-ROOF® is the latest technology in roof ventilation for Fielders® steel roofs. VENT-A-ROOF® is a cost-effective, architecturally attractive solution for:
- Commercial buildings
- Light Industrial buildings
- Residential homes
- Sheds
VENT-A-ROOF® is a non-mechanical continuously operating, waterproof, cyclone-rated, metal roof ventilation system that provides a condensation management solution. Managing roof cavity condensation mitigates mould issues and contributes to improved health and safety in buildings across Australia.
Benefits of a VENT-A-ROOF®
- Improves roof ventilation with continuous airflow, reducing both roof space temperature and energy costs associated with cooling the building
- Full roof ventilation is made possible with both ridge and hip vents
- Mitigates condensation, humidity and mould
- Australian wind, bushfire and cyclone rated
- Cost-effective and integrated into the roof providing a low profile attractive alternative to ventilators
- Keep cooler in summer and remove condensation in winter
- Certified for use in BAL 12.5 – 40 regions to prevent ember ingress at ridge and hips
- Certified for use in cyclonic regions
- DTC solution for 2019 NCC condensation management and roof ventilation requirements
How the system works
Figure 1.1
This deceptively simple passive system allows fresh outside air to be taken into the roof space either through soffit/eave vents or in through the system itself. This cooler air rises from these intake points and mixes within the ceiling or building space to create a natural flow of air that leaves the hot air escaping through the top of the ridge/skillion.
Simultaneously, external breezes provide a positive airflow which crosses over the ridge of the house creating negative pressure which pulls air out from the ridge vent. Effectively, two thermal effects create a continuous flow of air, allowing cool air into the roof/building space whilst extracting hot air.
This information is a guide to the design and installation of the VENT-A-ROOF® system for steel roofing and walling manufactured by Fielders®. We intend that it be used by all trades and professions involved with specifying and applying the VENT-A-ROOF® range of products.
We refer only to genuine steel roofing and walling manufactured by us and marketed under our brand names. Our recommendations should only be used for our products because they are based on comprehensive testing of our profiles, base metal thicknesses (BMT) and material finishes. More general design in installation with regard to steel cladding may be found in the Fielders® Roofing and Walling Installation Manual. This manual covers a range of topics not covered in this installation.
This information has been prepared for the VENT-A-ROOF® system for roofing applications using components manufactured or supplied by Fielders®.
Whilst this information primarily deals with VENT-A-ROOF® in roofing applications the principles apply equally to walling applications. For specific walling advise speak with your local Fielders® branch. VENT-A-ROOF® louvres are not recommended for use at wall bases where they may be subjected to constant moisture.
This page covers installation procedures for both new and retro fit applications in both non-cyclonic and cyclonic applications.
All erection and connection details are to be made in accordance with the relevant standard connection details contained in this page. We recommend you get professional advice to ensure your particular needs are adequately met.
To ensure maximum lifespan of your building, consult your nearest Fielders® branch for information regarding maintenance, handling, storage and any other technical assistance you may require.
Further information on products and service
Visit our website contact page for your local supplier of Fielders® products.
Design Preliminaries
Materials and finishes
VENT-A-ROOF® components and Fielders® cladding and flashings are manufactured from Australian made BlueScope steel.
Material specifications
VENT-A-ROOF® steel vent components are manufactured from 0.4mm BMT aluminium/zinc/magnesium alloy coated steel.
Fielders® steel cladding and flashings are available in a range of materials and finishes including
- Next generation ZINCALUME® aluminium/zinc/magnesium alloy coated steel complying with AS 1397:2011 G300, AM125 125g/m2 minimum coating mass.
- COLORBOND® steel is pre-painted steel for exterior roofing and walling. It is the most widely used. The painting complies with AS/NZS 2728:2013 and the steel base is an aluminium/zinc alloy-coated steel complying with AS 1397:2011. Minimum coating mass is AM100 (100g/m2).
- COLORBOND® Metallic steel is pre-painted steel for superior aesthetic qualities displaying a metallic sheen.
- COLORBOND® Ultra steel is pre-painted steel for severe coastal or industrial environments (generally within about 100m - 200m of the source). The painting complies with AS/NZS 2728:2013 and the steel base is an aluminium/zinc alloy-coated steel complying with AS 1397:2011. Minimum coating mass is AM150 (150g/m2).
- VENT-A-ROOF® louvres are not recommended for use with SuperDura™ Stainless steel
NCC roof space ventilation requirement V ventilation performance
Volume 1 of the National Construction Code (NCC) covering class 2-9 buildings (Non-Residential) outlines requirements for ventilation of roof spaces at;
Section F - Heath and amenity, Part F6 - Condensation management Performance requirements, Clause F6.4 – Ventilation of roof spaces (extract at Figure 2:1).
Similarly, Volume 2 of the NCC covering class 1 & 10 buildings (Residential) outlines ventilation of roof spaces at;
Section 3 - Acceptable Construction, Part 3.8 - Health and Amenity, Part 3.8.7 - Condensation Management, Clause 3.8.7.4 - Ventilation of roof spaces.
Roof ventilation requirements for both Residential and non-Residential buildings are similar in that where an exhaust system from a kitchen, bathroom sanitary compartment or laundry discharges into a roof space that roof space must be ventilated to outdoor air through evenly distributed openings.
The required ventilation openings must have a total unobstructed area of:
- For roof pitch of greater than > 22 degrees - an unobstructed area of 1/300 of the ceiling area.
- For roof pitch of less than < 22 degrees - an unobstructed area of 1/150 of the ceiling area.
- At least 30% of the total unobstructed area must be located not more that 900mm below the ridge/hip with the remaining required area provided by eave vents.
Figure 2.1:
NCC Volume 1 Extract
F6.3 Flow Rate and discharge of exhaust systems
a) An exhaust system installed in a kitchen, bathroom, sanitary compartment or laundry must have a minimum flow rate of:
1. 25 L/s for a bathroom or sanitary compartment;
2. and 40 L/s for a kitchen or laundry
b) Exhaust from a kitchen must be discharged directly or via a shaft or duct to outdoor air
c) Exhaust from a bathroom, sanitary compartment, or laundry must be discharged:
1. directly or via a shaft or duct to outdoor air; or
2. to a roof space that is ventilated in accordance with F6.4.
F6.4 Ventilation of roof spaces
a) Where an exhaust system covered by F6.3 discharges directly or via a shaft or duct into a roof space, the roof space must be ventilated to outdoor air through evenly distributed openings.
b) Openings required by a) must have a total unobstructed area of 1/300 of the respective ceiling area if the roof pitch is greater than 22˚, or 1/150 of the respective ceiling area if the roof pitch is less than or equal to 22˚.
c) 30% of the total unobstructed area required by b) must be located not more than 900 mm below the ridge or highest point of the roof space, measured vertically, with the remaining required area provided by eave vents.
NCC residential Deemed-to-Satisfy Ventilation requirements (with eave vents) for Whirlybirds or VENT-A-ROOF®
Linear metres of VENT-A-ROOF® required | |||||
Roof pitch | Ceiling area (m2) | No. of 300mm diameter whirlybirds | No. of 400mm x 200mm eave vents | Skillion ridge ventilation (lm) | Gable/hip ventilation (lm) |
≤22° | 100 | 3 | 7 | 22 | 11 |
125 | 4 | 9 | 27 | 14 | |
150 | 5 | 10 | 32 | 16 | |
175 | 5 | 12 | 37 | 19 | |
200 | 6 | 14 | 43 | 22 | |
225 | 7 | 15 | 48 | 24 | |
250 | 8 | 17 | 53 | 27 | |
275 | 8 | 19 | 58 | 29 | |
300 | 9 | 20 | 64 | 32 | |
325 | 10 | 22 | 69 | 35 | |
350 | 10 | 24 | 74 | 37 | |
400 | 12 | 27 | 85 | 43 | |
>22° | 100 | 2 | 4 | 11 | 6 |
125 | 2 | 5 | 14 | 7 | |
150 | 3 | 5 | 16 | 8 | |
175 | 3 | 6 | 19 | 10 | |
200 | 3 | 7 | 22 | 11 | |
225 | 4 | 8 | 24 | 12 | |
250 | 4 | 9 | 27 | 14 | |
275 | 4 | 10 | 29 | 15 | |
300 | 5 | 10 | 32 | 16 | |
325 | 5 | 11 | 35 | 18 | |
350 | 5 | 12 | 37 | 19 | |
400 | 6 | 14 | 43 | 20 |
NCC residential Deemed-to-Satisfy Ventilation requirements (without eave vents) for Whirlybirds or VENT-A-ROOF®
Linear metres of VENT-A-ROOF® required (No Eave Vents) |
||||
Roof pitch | Ceiling area (m2) | No. of 300mm diameter whirlybirds | Skillion ridge ventilation | Gable/hip ventilation |
≤22° | 100 | 10 | 71 | 36 |
125 | 12 | 88 | 44 | |
150 | 15 | 106 | 53 | |
175 | 17 | 123 | 62 | |
200 | 19 | 141 | 71 | |
225 | 22 | 158 | 79 | |
250 | 24 | 176 | 88 | |
275 | 26 | 193 | 97 | |
300 | 29 | 211 | 106 | |
325 | 31 | 228 | 114 | |
350 | 33 | 248 | 123 | |
400 | 38 | 281 | 141 | |
>22° | 100 | 5 | 36 | 18 |
125 | 6 | 44 | 22 | |
150 | 8 | 53 | 27 | |
175 | 9 | 62 | 31 | |
200 | 10 | 71 | 36 | |
225 | 11 | 79 | 40 | |
250 | 12 | 88 | 44 | |
275 | 13 | 97 | 49 | |
300 | 15 | 106 | 53 | |
325 | 16 | 114 | 57 | |
350 | 17 | 123 | 62 | |
400 | 19 | 141 | 71 |
For residential buildings outside of the m2 range in the above tables, the calculation example below maybe used.
Calculation example for a “typical” residential building with bathrooms and kitchen exhaust vans venting into roof space.
House ceiling m2 = 250m2
Roof pitch = 22.5 degrees
Therefore,
250m2 ceiling area x requirement > 22 degree roof pitch i.e. 1/300 (0.003) = 0.833m2 of ventilated opening. This may be split 30/70 between ridge and eave vents
Therefore,
0.833m2 x 30% = 0.250m2 ridge vent
0.833m2 x 70% = 0.583m2 eave vents
Ventilation capacities
- 1m of VENT-A-ROOF® ridge provides 0.019008m2 of unobstructed area for ventilation.
- Generally, a 300mm dia whirlybird (WB) provides an unobstructed area for ventilation of 0.07m2 ea.
- A 400mm x 200mm eave vent (EV) will provide 0.08m2 of unobstructed area for ventilation.
Airflow Calculations
Single storey house | Wind Pressure Pa | Wind speed | External air temp differential to attic space air temp (degrees Celsius | 300mm whirlybird | lm VENT-A-ROOF® louvre skillion ridge (with 45-50mm throat dimension) | lm VENT-A-ROOF® louvre Gable/ Hip Ridge (2m of louvre) (with 45-50mm throat dimension) | lm VENT-A-ROOF® louvre skillion ridge = 1x300mm whirlybird | lm VENT-A-ROOF® louvre gable/hip ridge (2m of louvre) |
||||||
km/h | Knots | Airflow (m3/s) | Heat Extraction (kW | Airflow (m3/s) | Heat Extraction (kW | Airflow (m3/s) | Heat Extraction (kW | Airflow (m3/s) | Heat Extraction (kW | Airflow (m3/s) | Heat Extraction (kW |
|||
0 | 0 | 0 | 6 | 0.019 | 0.137 | 0.006 | 0.046 | 0.013 | 0.091 | 3 | 3 | 1.5 | 1.5 | |
12 | 0.020 | 0.288 | 0.007 | 0.096 | 0.013 | 0.092 | 3 | 3 | 1.5 | 1.5 | ||||
18 | 0.021 | 0.454 | 0.007 | 0.151 | 0.014 | 0.302 | 3 | 3 | 1.5 | 1.5 | ||||
40 | 0.022 | 1.056 | 0.007 | 0.352 | 0.015 | 0.704 | 3 | 3 | 1.5 | 1.5 | ||||
2.0 | 6 | 3.2 | 6 | 0.029 | 0.206 | 0.01 | 0.069 | 0.019 | 0.138 | 3 | 3 | 1.5 | 1.5 | |
12 | 0.030 | 0.429 | 0.01 | 0.143 | 0.020 | 0.286 | 3 | 3 | 1.5 | 1.5 | ||||
18 | 0.031 | 0.677 | 0.01 | 0.226 | 0.021 | 0.451 | 3 | 3 | 1.5 | 1.5 | ||||
3.6 | 8 | 4.3 | 6 | 0.034 | 0.247 | 0.011 | 0.082 | 0.023 | 0.165 | 3 | 3 | 1.5 | 1.5 | |
12 | 0.035 | 0.5 | 0.012 | 0.167 | 0.023 | 0.333 | 3 | 3 | 1.5 | 1.5 | ||||
18 | 0.036 | 0.787 | 0.012 | 0.262 | 0.024 | 0.524 | 3 | 3 | 1.5 | 1.5 | ||||
8.0 | 12 | 6.5 | 6 | 0.051 | 0.37 | 0.017 | 0.123 | 0.034 | 0.246 | 3 | 3 | 1.5 | 1.5 | |
12 | 0.052 | 0.753 | 0.017 | 0.251 | 0.035 | 0.502 | 3 | 3 | 1.5 | 1.5 | ||||
18 | 0.053 | 1.137 | 0.018 | 0.379 | 0.035 | 0.758 | 3 | 3 | 1.5 | 1.5 | ||||
12.5 | 15 | 8.1 | 6 | 0.060 | 0.432 | 0.02 | 0.144 | 0.040 | 0.288 | 3 | 3 | 1.5 | 1.5 | |
12 | 0.060 | 0.871 | 0.02 | 0.29 | 0.040 | 0.58 | 3 | 3 | 1.5 | 1.5 | ||||
18 | 0.061 | 1.324 | 0.02 | 0.441 | 0.041 | 0.882 | 3 | 3 | 1.5 | 1.5 | ||||
14.2 | 16 | 8.6 | 6 | 0.063 | 0.456 | 0.021 | 0.152 | 0.042 | 0.304 | 3 | 3 | 1.5 | 1.5 | |
12 | 0.065 | 0.935 | 0.022 | 0.312 | 0.043 | 0.623 | 3 | 3 | 1.5 | 1.5 |
• Increasing wind speeds will cool a sunlit roof hence reductions in attic v ambient temperatures for higher wind speeds.
• Bolded text represents default Australian design pressure of 12.5 Pa.
Airflow capacity/air exchange calculation example for a "typical" light industrial shed
Shed Dimensions
Length50m
Width 18m
Wall height at eave 3m
Roof pitch 5 degrees
Roof Apex height 3.790m
Wind speed Default design pressure 12.5pa or 8.1knots
External v internal air temp 12 degrees – warm day
Calculation
Step 1 – Shed Air Volume
- Air volume of shed = (50m x 18m x 3m) + (50m x 9m x 0.790m) = 2700 + 355.5 = 3055.5m3
Step 2 – Air Extraction RateFrom
- Table 3 we can see that the Airflow/Air Extraction Rate per metre of louvre at the ridge given a 12 degree external to internal temperature variation and 8.1knts of wind = 0.040m3/s
Step 3 – Air Volume Extracted per Hour
- 0.040m3/s per metre of louvre
50m building length = 2m3/secondx
60 seconds = 120m3/minx
60 minutes = 7200m3/hr
Step 4 – Air Exchange Rate
- Shed air volume = 3055.5m3
- Volume extracted per hour = 7200m3
Therefore:
3055.5m3 divided by 7200m3/hr airflow provides for complete shed air changeover every .424 hours or every 25 minutes from the VENT-A-ROOF® system alone.
In practice, additional air changeover will occur via doorways, windows, shed wall to roof junctions etc.
VENT-A-ROOF® BAL (Bushfire Attack Level) performance
All new residential construction in Australia must undergo a BAL (Bushfire Attack Level) assessment as part of the building application process.
Properties are assessed against 6 Bushfire Attack Levels as outlined in the table below
Bushfire Attack Levels
Bushfire Attack Level (BAL) | BAL zone description |
BAL Low | There is insufficient risk to warrant specific construction requirements |
BAL – 12.5 | Ember attack. (BAL 12.5 Construction Requirements) i.e. Non-combustible coverings roof/wall junction sealed. Openings fitted with non-combustible ember guards. Roof to be fully sarked |
BAL – 19 | Increasing levels of ember attack and burning debris ignited by windborne embers, together with increasing heat flux. (BAL 19 Construction Requirements) i.e. Non-combustible coverings roof/wall junction sealed. Openings fitted with non-combustible ember guards. Roof to be fully sarked |
BAL – 29 | Increasing levels of ember attack and burning debris ignited by windborne embers, together with increasing heat flux. (BAL 29 Construction Requirements) i.e. Non-combustible coverings roof/wall junction sealed. Openings fitted with non-combustible ember guards. Roof to be fully sarked |
BAL – 40 | Increasing levels of ember attack and burning debris ignited by windborne embers, together with increasing heat flux and with the increased likelihood of exposure to flames. (BAL 40 Construction Requirements) i.e. Non-combustible coverings roof/wall junction sealed. Openings fitted with non-combustible ember guards. Roof to be fully sarked and no roof mounted evaporative coolers |
BAL – FZ | Direct exposure to flames from fire, in addition to heat flux and ember attack. (BAL FZ Construction Requirements) i.e. Roof with FRL of 30/30/30 or tested bushfire resistance to AS1530.8.2. Roof/wall junction sealed. Openings fitted with non-combustible ember guards. No roof mounted evaporative coolers |
VENT-A-ROOF® has been independently assessed as suitable ridge and hip treatment to prevent ember ingress for BAL-12.5 – BAL – 40 zones
Fielders® steel cladding and ancillary products combustibility status are outlined in NCC compliance documents located at https://specifying.fielders.com.au/roofing-walling/design-data/statement-of-compliance-for-fielders-roofing-walling-and-rainwater-goods/
VENT-A-ROOF® cyclonic performance
Air leakage testing conducted at Farabaugh Engineering and Testing, show that VENT-A-ROOF® assists pressure equalisation between internal and external pressures. Testing results as shown in the below table, demonstrate that a greater volume of air “escapes” through the VENT- A-ROOF® system than what is let in, an approximate 8% difference. The results show that as the test pressure increases, the rate of air escaping through the VENT-A-ROOF® system increases.
NB Test results Infiltration = air exiting the roof cavity and Exfiltration = air entering the roof cavity. (Nielson, 2019)
Test Pressure
Infiltration | Exfiltration | Ratio (%) | ||||||
Test Pressure (Psf) | Test Pressure (Pa) | Air leakage rate (Cfm) | Air leakage rate (m3/s) | Air leakage rate (Cfm) | Air leakage rate (m3/s) | Infiltration | Exfiltration | Difference (m3/s) |
1.57 | 75.17 | 44 | 0.020765688 | 37.5 | 0.017698029 | 54% | 46% | 0.003067658 |
6.24 | 298.77 | 86.1 | 0.040634675 | 74.5 | 0.035160085 | 54% | 46% | 0.00547459 |
Based on these results, it is determined that installation of the VENT-A-ROOF® system to ridgeline areas of metal clad roofing to residential and commercial properties, will reduce internal pressures and as such reduce structural loads to these structures during cyclonic and high wind events. (Nielson, 2019)
VENT-A-ROOF® has been independently assessed and certified as suitable for use in cyclonic regions when affixed in accordance with the VENT-A-ROOF® Design and Installation Guide for cyclonic regions.
Installation - New Installations
Step 1 - Roof Sheeting Installation
Install Fielders® S-Rib™, Fielders® TL-5™ or Fielders® KingKlip®700 sheeting in accordance with installation details available on this website.
Critical dimensions for roof ridge batten position and ridge throat dimensions are shown at Figure 3.1.1.
Figure 3.1.1
Fielders® Roll Top Ridge
Dimensions (mm) | ||||||||
Batten | Sheet | Throat | Ridge | |||||
Apex ridge to toe of batten | Sheet overhang top of batten | Sheet to sheet | Ridge legs | |||||
15˚ | 22.5˚ | 25˚ | Toe | Step/Raise | Pan | |||
State | A | B | C | E | F | G | ||
NSW | 175 | 165 | 160 | 95 | 60-55 | 17.5 | 25 | 106 |
VIC | 175 | 170 | 165 | 90 | 55-50 | 17.5 | 25 | 102 |
TAS | 175 | 170 | 165 | 90 | 55-50 | 17.5 | 25 | 102 |
SA | 165 | 155 | 150 | 91 | 30-17 | 12 | 22 | 91 |
WA | 170 | 160 | 155 | 95 | 50-45 | 20 | 25 | 99 |
Figure 3.1.2
Fielders® Folded Ridge
Dimensions (mm) | |||||||||
Batten | Sheet | Throat | Ridge | ||||||
Apex ridge to toe of batten | Sheet overhang top of batten | Sheet to sheet | Ridge legs | Feed width |
|||||
15˚ | 22.5˚ | 25˚ | Toe | Step/Raise | Pan | ||||
Region | A | B | C | E | F | G | (mm) | ||
Non cyclonic | 180 | 175 | 170 | 95 | 55-65 | 22 | 25 | 150 | 400 |
Cyclonic | 205 | 200 | 195 | 95 | 100-110 | 22 | 25 | 175 | 45 |
Figure 3.1.3
Fielders® Folded Ridge (Commercial applications)
Dimensions (mm) | |||||||||||
Batten | Sheet | Throat | Ridge | ||||||||
Apex ridge to purlin edge | Sheet overhang top of Purlin | Sheet to sheet | Ridge barge legs | Feed width |
|||||||
1˚ | 5˚ | 15˚ | 1˚ | 5˚ | 15˚ | Toe | Step/Raise | Pan | |||
Application | A | B | C | E | F | G | (mm) | ||||
Commercial/Industrial | 173 | 95 | 110 | 140-180 | 22 | 25 | 200 | 500 |
Figure 3.1.4
Skillion Roof Ridge/Apron
Dimensions (mm) | |||||||||
Batten | Sheet | Throat | Ridge Barge/Apron | ||||||
Apex ridge to toe of batten | Sheet overhang top of batten | Sheet to sheet | Ridge barge legs | ||||||
15˚ | 22.5˚ | 25˚ | Toe | Step/Raise | Pan | Wall side | |||
Region | A | B | C | E | F | G | H | ||
Non cyclonic | 190 | 185 | 180 | 95 | 40-35 | 25 | 25 | 150 | 75 |
Cyclonic | 240 | 235 | 230 | 95 | 90-85 | 25 | 25 | 200 | 75 |
It is important that a consistent line is maintained at the ridge line of sheeting as per the dimensions noted in Figure 3.1.1-3.1.4 and the above tables as appropriate. Do not screw fix the ridge line of roof sheets. Sheet pans should not be turned up.
Step 2 - Begin VENT-A-ROOF® louvre install
Looking at ridge or hip line, begin the installation of VENT-A-ROOF® louvres from left to right.
For hipped roofs where only ridge potions of the roof are to be vented, start installation of the VENT-A-ROOF® louvres at the crown point of the roof.
Step 3 - Slide louvre over sheet
Slide VENT-A-ROOF® louvre over the end of metal sheet.
Step 4 - Fix louvre to sheet
At the left end of louvre, apply enough pressure that the metal sheeting embeds a minimum of 3mm into the foam. To hold louvre into place, install one screw (10-16 x 16mm Teks® screw minimum class 3 coating) through the top of louvre into the rib of sheeting.
Continue installing the louvre from left to right screwing the top line of the louvre first. Ensure the louvre is pulled tight when installing the 10-16 x16mm Teks® screws so that the sheet is embedded a minimum of 3mm into the foam.
Finish screw placement through the louvre. Screws are to be installed as per screw pattern shown at Louvre fixing screw pattern - Cyclonic and Non Cyclonic applications table. Install full sealant bead to the end of louvre and foam.
Step 5 - Add additional louvres
Slide next length of louvre at an angle overlapping and insert it into the crimped end of the installed louvre, making sure the sealant and foam make good contact to ensure a weather-tight seal.
While fitting the louvre against previous louvre, ensure that the foam is in place and against metal sheeting. Screw in place as done in Steps 3 - 5.
Continue along the ridge, repeating Steps 3 - 5.
Step 6 - Install ridge cap
Install ridge cap in accordance to AS 1562.1 using screws recommended at Specifying.Fielders.com.au Screws should penetrate ridge, VENT-A-ROOF® louvre, roof sheet and batten below providing fixing to both roof ridge and ridge cap.
No scribing is required with VENT-A-ROOF® louvre, due to the closed cell weather tight foam within the VENT-A-ROOF® louvre.
For applications where only the ridge portion of the roof is utilising VENT-A-ROOF® the VENT-A-ROOF® ridge will sit 25mm above the hips caps. This will allow the VENT-A-ROOF® roll top ridge to neatly marry to the hip roll top ridge as shown in Figure 3.6.1.
Please note that for South Australian applications utilising roll top ridge that some pressure is required to “spread” the roll top ridge to cover the VENT-A-ROOF® louvres and maintain ridge throat dimension.
Hip install
The same principles apply to installation of hips with critical dimensions being identical.
Screw pattern
Cyclonic and Non Cyclonic
Louvre fixing screw pattern - Cyclonic and Non Cyclonic applications
Fielders® | |||||
Sheet Type | S-Rib™ | TL-5™ | KingKlip®700 | Screw | |
Recommended spacing of VENT-A-ROOF® fixing screws | 1st and last sheet rib | 10 - 16 x 16mm Teks® |
|||
then every 4th rib | then every 2nd rib | then every rib | |||
Distance from front/bottom edge of VENT-A-ROOF® louvre | 60mm | ||||
Distance from top edge of VENT-A-ROOF® louvre | 25mm | ||||
Fixing spacing at VENT-A-ROOF® joints | Both sides of join | ||||
Spacing of ridge cap fixing screws | Every 2nd rib | Every rib | Every rib | As per Fielders® published data for roof sheeting |
|
for cyclonic applications cyclonic zips should be used for ridge cap fixing screws |
Installation - Retro-Fit
The vast majority of Australia’s existing residential and light commercial and industrial buildings do not comply with the current NCC specification for roof ventilation.
Installation of a VENT-A-ROOF® system to an existing building can provide immediate benefits to health and amenity of the building by improving condensation management and reducing thermal loads within the roof space and thus living space.
Step 1 - Determine replacement ridge flashing dimensions
Remove a small number of screws from a portion of the exist ridge to allow measurement from the ridge screw line (and mid-line of existing batten) to the top of the existing sheets.
Compare the measured dimensions with those in Table 6 to determine if roll top ridge or a special folded ridge is required.
Measure and order ridge lengths and VENT-A-ROOF® louvres.
Step 2 - Remove existing ridge
Remove the portion of the existing ridge to be replaced by the VENT-A-ROOF® system to expose the ridge throat.
Step 3 - Mark roof sheets to be cut
From the calculations determined in Step 1 mark each end of the ridge to be cut. Using a chalk line ping a line across the ridge in preparation to cut the sheets back.
Step 4 - Cut back the sheets
Using a cold cut steel saw, excalibur shears or similar cut back the roof sheets and cut back any insulation or sarking to reveal throat gap.
Step 5 – Install VENT-A-ROOF® louvres
Start laying VENT-A-ROOF® louvres, left to right, as per 3.2 through to 3.10 of new installation instructions following appropriate screw patterns.
Step 6 – Install new ridge flashings
Following guidelines from 3.10 cut and screw fix new ridge flashings to vented ridge.
Step 7 – Clean up
Clean all debris from roof paying particular attention to swarf from cutting of sheets and screw installation.
Step 8 – Install eave vents
Install 400mm x 200mm eave vents, if required, in accordance with manufacturer’s instructions.
Warranties
Fielders® operations have been servicing Australia’s residential, industrial and commercial construction industries for over 115 years. Fielders® unique and innovative products, first class engineering and testing resources as well as a strong commitment to quality customer service and support make them leaders in metal roll-forming manufacture and supply.
Our products are engineered to perform according to our specifications only if they are used in the appropriate conditions and installed to the recommendations in this information and our other publications.
Naturally, the warranties require specifiers and installers to exercise due care in how the products are applied and installed and are subject to final use and installation. Also, owners need to maintain the finished work. The VENT-A-ROOF® system will not negatively impact warranties applicable to Fielders® products.
We invite you to ask about the warranties applicable to your proposed purchase, at your supplier of Fielders® products.
Conditions of use
If you use this information, you acknowledge and agree that your use is subject to the terms and conditions in this information. Fielders®, its agents, officers, employees, sub-contractors or consultants make no representations, either expressed or implied, as to the suitability of the information and data in this page for your particular purposes.
It’s your responsibility to ensure the design you use is appropriate for your needs, the products you have purchased, your site and structural limitations and your building and construction capabilities.
This information endeavours to present information on products, details, installation and practices in a clearly prescribed manner and it is the user’s responsibility to apply the information in the way intended. If there is any uncertainty then it is the user’s responsibility to seek clarification.
Where we recommend use of third-party materials, ensure you check the qualities and capabilities of those products with the relevant manufacturer before use.
Use of genuine materials
Structures in this information should only be built or constructed using genuine Fielders® or recommended third party products. Except as otherwise provided in these terms, any warranties only apply to you (if at all) if you use the recommended genuine Fielders® or third-party products and method of construction.
Check delivery
It is important that you check all materials delivered to site against your invoice before you use them in your building or construction to ensure all components have arrived, are of the appropriate quality and are ready for installation.